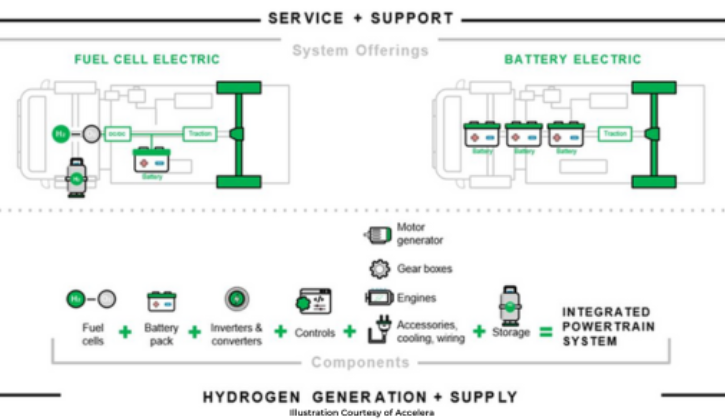
Part 3 of a 3-part series with Accelera™ by Cummins. This interview was conducted with team members of Accelera who shared with us the technical aspects of FCEV, but moreover, where they see it being applied in the future. This article, in no way, should be considered an endorsement of Cummins and/or Accelera or its EV/alt-fuel products. It is simply observations and information as a result of Cummins’ willingness to share information with ACT’s staff.
What is ACT doing?
As is the rest of the commercial vehicle (CV) industry, ACT Research is looking at the road ahead. We've taken our expertise and first-hand knowledge from more than 50 players in the market to develop CHARGING FORWARD: 2023-2040 Decarbonization Forecast & Analysis (available now) and NA CV OUTLOOK Plus (available January 2024). Read more about how ACT views the future of commercial vehicles at the end of this article or by clicking the button below.
Common topics of discussion, with both perspectives, for FCEVs:
- What about refueling?
- Will larger tanks be required?
How can I mitigate potential tire wear from the instant torque?
- Will diesel's cost advantage today be sustainable in the future?
- What secondary market value might exist?
- How does regenerative braking play a role in FCEV adoption?
- Where do we get the hydrogen fuel?
These topics and more are covered in part 3.
In part 1 of this series, ACT provided in-depth observations on battery-powered cargo trucks and yard tractors. The goal of the series is and was to provide first-hand observations based upon discussions with engineers and ride alongs with prototypes to answer reader questions. What are these vehicles really like to operate? How might they fit into your operations?
Part 2 of this series concentrates on what hydrogen (H2)-fueled internal combustion engine (ICE) alternatives have to offer. What can one expect and what are the unknowns?
Part 3 of this series concentrates on what fuel cell electric vehicle (FCEV) alternatives have to offer. What can one expect and what are the unknowns? To prepare, we spent time with Accelera™ by Cummins team members who shared with us the technical aspects of FCEV, but moreover, where they see it being applied in the future.
Following Promising Paths Forward
Customers will have a choice of power in the future. One path to decarbonization is the traditional ICE and the other is an alternative, zero-emissions form of power.
The customer’s choice leads to a series of decisions. What is the product? What is the channel of distribution? What is the promotion, etc.? ACT has been providing answers and direction about what power will be available in the future and what might be the right choice for your particular operation.
Much of the information needed to make that choice is not currently clearly in sight, just over the horizon. One path toward decarbonization reduces the emissions from ICE, while the other eliminates combustion and emissions created through the combustion process. Each path has associated costs, required changes in daily operations, probability of successful adoption, and time required for success. Being an early adopter is no guarantee of success, but being late in the decision-making process can have dire consequences.
We know much more about the ICE path. Diesel engines are cleaner than ever and will be even cleaner with the new diesel emission standards. Cleaner NG is already available with higher horsepower versions soon to arrive. Renewable NG (RNG) is another promising path to zero-emissions fuel. Truck chassis really won’t change much with the adoption of these cleaner alternatives. The engine is in the front of the vehicle, followed by the clutch, transmission, and rear axle. The fuel tanks may be different, but overall, the vehicle is pretty much the same. The zero-emissions path will have fuel cells, hydrogen tanks, electric drives, and a host of other changes that are not conventional. What ACT has attempted to do with this “Alternative to Diesel” series is provide insight to give you a competitive advantage as you contemplate these changes to your operations.
Where does ACT get its information? ACT has a special connection with transportation industry leaders, from OEMs to major suppliers to fleets and leasing organizations of all kinds. One of those relationships is with Cummins and Accelera, particularly their engineering and support staff, with whom we’ve been able to discuss these new technologies, get answers to our technical questions, and gather information our readers need to know to help them make immediate and future business decisions about alternative power. One of the reasons we spoke with Accelera is their “big picture” and agnostic view of many technologies.
On one hand, Cummins continues to work on traditional ICE alternatives with new offerings of NG and hydrogen-fueled engines. Cummins has covered the other path with the announcement of its fifth operating segment, Accelera, which provides zero-emissions technologies such as battery-electric and fuel cell-electric powertrain solutions, along with electrolyzers for green hydrogen production. For Cummins, Accelera is a key part of their “Destination Zero” strategy. The strategy is rooted in the understanding that multiple solutions are required to achieve industry-wide decarbonization across diverse applications. The company has no illusions that the change in fuels will be a light-switch event, but rather a destination with early adopters, a messy middle, and a wide variance by countries and global regions.
So, what is a hydrogen FCEV? FCEVs use a propulsion system like that of battery-electric vehicles (BEVs), where energy stored as hydrogen is converted to electricity by the fuel cell capable of providing direct electricity to the electric motor(s) while in operation. Basically, it is a BEV that has a combined H2 fuel tank and fuel cell engine that converts H2 and oxygen to produce electricity and water. It is able to keep the battery charged and provide direct electricity for the traction system. The FCEV uses the same components as a BEV but adds the fuel cell and H2 fuel tank. The hydrogen is stored on board in high pressure tanks much like a NG-fueled truck. You can review the basics of H2 ICE and BEV by clicking HERE.
FCEVs can travel the highways just as any diesel, NG, or H2-fueled ICE-powered truck can. The FCEV can refuel at any truck stop offering hydrogen fuel or a behind-the-fence operation just as an ICE-powered vehicle would. There is one BIG difference in the operation of the two types of vehicles, and it is why the FCEV shows so much promise. The basic difference is that there is no combustion with the FCEV, and thus, no emissions. Let that sink in for a minute. No matter what we do with diesel fuel, NG, H2, or any other fuel that is burned in a combustion chamber, while low, we still get emissions. Yes, we use particulate traps, three-way catalysts, diesel exhaust fluid (DEF), and who knows what else when we get to the 2027 emission standards, but in each case, we must deal with the byproducts of combustion. With a hydrogen fuel cell, the energy we need comes from a chemical reaction and not combustion, so there is nothing from the tailpipe except water vapor. The hydrogen fuel cell generates the electricity to the electric motor(s) propelling the truck and the cargo down the road. The basic design is simple, but the execution is complex.
The execution of the design is the “science of compromise.” We have many options for putting a FCEV together, and along the way, we must make compromises. Will the electric motor(s) be mounted at one or more of the drive wheels, or will we use a driveshaft from an electric motor to a conventional rear axle design? Where will we place the primary electric battery? How big does it need to be in terms of power output? How heavy a load are we going to be pulling? What is the maximum grade we will need to pull and at what minimum speed? After we make those decisions, we will have a better idea of how big our fuel cell needs to be in terms of power output to provide the electric power to the vehicle. Then we’ll need to decide how far we want the vehicle to go before we need to refuel. Since the hydrogen fuel needs more volume than weight, our hydrogen fuel tanks will take up more room on the vehicle, as well as weight, than conventional diesel fuel tanks to go the same distance. When all of the above decisions have been made, we can figure out how we will get all of the components into the basic vehicle as we know it today.
With a pure BEV, the battery is sized to match the vehicle’s duty cycle. FCEVs are designed to be capable of providing primary power to the electric motor(s) to achieve vehicle duty cycle performance requirements, while additional battery electric power can be used to help manage through transients or to create the most optimal TCO solution based on application requirements. The whole process is similar to spec’ing a diesel truck. How much power do we need and how much diesel fuel are we going to have in the tanks? In general, we can use a smaller sized battery than in a BEV, because we have the hydrogen fuel cell to provide the extra mileage “energy” that we need.
As with the BEV, the noise of a hydrogen-fueled vehicle is different than that of an ICE vehicle. You will hear the noise of some pumps, switches making contact, etc., but not the sound of combustion taking place. Again, as with a BEV, a separate electrical system will be used for the vehicle lights, A/C and heating systems, and other electrical systems just as on an ICE vehicle. Why redesign all the electrical components on a conventional ICE truck to match a high voltage battery when a simple 12-volt system will do?
The engineer’s goal is to make refueling time equal to diesel, and they are making progress. Any current gap in refueling times should be considered a temporary gap. Remember, besides the diesel fuel, we may need to refuel the DEF tank, which takes additional time. It will take incremental time to fill the hydrogen tanks, like what happens today with the NG refueling process.
A typical FCEV will weigh more than a comparable spec’d diesel-fueled tractor. However, the maximum payload of a typical FCEV tractor-trailer will be in a neighborhood comparable to diesel. This is not a show stopper, as 70% of the tractor-trailers on the road today “cube out” (the trailer is full and no more freight can be loaded) as opposed to 30% of units that “gross out” (the combined weight of the tractor-trailer is at the maximum legal weight). FCEV will receive a weight exemption, much like that of a NG-powered unit, which in some states gets an extra 2,000 pounds, so the FCEV would be competitive with a traditional diesel-fueled tractor. What happens in those states where ICE-powered tractors are banned? It won’t make any difference whether you “cube out” or “gross out,” you will need to consider alternative power.
Maintenance will be a little different for a FCEV than for a typical diesel tractor. Some things will stay the same, such as tire and brake changes. Clutch and transmission rebuild and adjustments will be a thing of the past, as will work on DEF systems, catalysts, and particulate filters. Some operations will be completely new, such as electric drive motor maintenance and repair/rebuild. Basically, FCEV maintenance will be the same as that for a BEV, with the addition of the hydrogen fuel cell. There may be a requirement for fire suppression equipment because of the nature of hydrogen, but many shops that have run NG-fueled equipment already have experience.
The fuel cell will mix the hydrogen with oxygen in the air to get the electrical power we need, as well as a little heat and a little water vapor. The air must be clean…really clean…so as not to get any impurities into the polymer electrolyte membrane (PEM) where the chemical process takes place. The PEM is a very thin solid organic compound, about as thin as a couple sheets of paper, where the ion exchange takes place. The membrane must be kept moist for particles to pass through it. This article won’t delve deep into the physics of how a fuel cell works, except to say that the process is well understood and used in many applications.
A fuel cell engine has similarities to a diesel engine as they both have fuel systems, air handling systems, thermal management systems, and control systems. While a diesel engine has combustion, a fuel cell has a stack comprised of many cells executing the electrochemical process of converting hydrogen fuel to electricity. The size of the stack correlates to the electrical power output. The individual fuel cells are combined into a series of fuel cells called a “stack” to get a higher voltage power unit than an individual cell. So, the “stack” may consist of hundreds of individual fuel cells to get a much higher voltage, sizing it to meet driver demand and heavy-duty commercial application power requirements.
As with anything new, there are several hurdles that require a change in thinking. As such, some may say FCEV will never be accepted. Here are several common topics of debate, with both perspectives, for FCEVs:
- There aren’t many refueling stations today. The full infrastructure won’t appear overnight, but with dedicated routes, or routes with appropriate mileage constraints, the ecosystem could be developed for range viability. If hydrogen, particularly clean hydrogen (not made from fossil fuels), is developed for other purposes, the “ecosystem” can develop that much faster for trucks. Remember how quickly DEF became available at the diesel pumps.
- Trucks will need larger fuel tanks than traditional diesel! Yes, they will; hydrogen has lower volumetric energy density than diesel. Thus, you need more on board, meaning more space consuming high-pressure tanks. The problem was overcome with natural gas, and hydrogen will follow a similar model.
- With the instant torque the electric motor(s) provide, tire wear can be a real problem! Tire costs per mile will be out of sight. The development engineers are on top of this problem, with the ability to control or limit the amount of power the electric motor(s) can provide at launch. The amount of power can be controlled. The logic of traction control is well understood. Thus, a BEV or FCEV can be programed to have the same acceleration characteristics as today’s diesel trucks.
- Won’t the operational costs for a hydrogen FCEV be higher than diesel? Perhaps, but with no combustion, there are no emissions except water vapor. With increased volumes, hydrogen FCEV costs will decrease. Diesel starts today with a cost advantage, but it faces significant cost hurdles in the future. Typically, a kg of hydrogen is compared to a gallon of diesel fuel. We could see fuel parity in the 2030s as the supply chain matures.
- Won’t FCEV life cycle cost be more? Initially yes, but there are some things to consider. A FCEV can replace the battery when their useful life in a truck is done, but they can still have value in a secondary market, such as for backup power for communities in case of emergencies. For diesel engines, what do you do with the engine or the truck when emissions must be maintained for a much longer period of time, as is being discussed with the new 2027 truck emission laws? How big will the diesel-powered used truck market be if there are some first owner and second owner emission requirements with associated costs? In the past, trucking companies have been able to pass new costs to consumers. Let us assume they will be able to do so in the future.
- It doesn’t have a Jake Brake option, so how do I slow the vehicle down and save on brake wear? No, it doesn’t have a Jake Brake, but it has regenerative braking that charges the battery and slows the vehicle down. The FCEV has the ability to “kinetically run” the electric motors in “generator mode” to charge the batteries and slow the vehicle by applying a retarding torque. The electric motors can generate electricity saving on hydrogen fuel.
- Where do we get the hydrogen fuel? The beauty of hydrogen fuel is that it can be generated from wind and solar sources, which is known as clean (or green) hydrogen. The green hydrogen fuel is created from electrolyzers where the electricity is created from these renewables. As mentioned previously, they are coming into use not just for trucks but for other purposes. Some generate hydrogen fuel from natural gas, others from other petroleum sources.
How does ACT view the future of powertrain alternatives?
While ACT remains fuel agnostic, and believes fleets know their operations better than anyone else, we also recognize ICE costs will rise as increased emissions regulations are globally adopted, and tougher regulatory standards for ICE will lead to a more favorable TCO for CEV. Most CVs are working in competitive situations, so questions on operating costs are fundamental. Will each powertrain alternative—EV, FCEV, H2 ICE, etc.—offer varying degrees of ROI? Yes. And, of course, this depends on each application's unique duty cycle. ACT Research uses a bottom-up approach, analyzing component costs, operational costs based on duty cycles, fuel costs, maintenance costs, taxes, infrastructure, and more.
In June 2023, our team published the third edition of CHARGING FORWARD, featuring additional powertrain analysis to our current battery and fuel cell electric to include natural gas, hydrogen, H2 ICE, gasoline, propane, and hybrid powertrain alternatives, forecasting the adoption rates of 52 vehicle applications across Classes 4-8 CVs in North America, Europe, and China. We've created this model to provide guidance for strategic business planning over the next 15 years, so your business is strongly positioned for a decarbonized future.
Want to learn more about ACT's CHARGING FORWARD? Complete the form at the bottom of this page.
Additional Resources
(This article, in no way, should be considered an endorsement of Cummis (Accelera) and/or its EV/alt-fuel products. It is simply a report on observations and education as a result of Cummins’ (Accelera) willingness to share information with ACT’s staff.)
CHARGING INTO TOMORROW:
Numerous articles have been written about the anticipated transition to electric trucks. There are all sorts of numerical models, projections, and opinions in favor of and against adoption. One wonders how many of those commentators have actually driven a battery powered commercial vehicle. With this question in mind, ACT undertook an initiative to get some first-hand observations by finding an operator of one or more electric trucks. The plan was not designed to be a data-driven road test, nor a comparison of one vehicle manufacturer with another, but rather to gather some first-hand observations with which readers could verify or refine their opinions.
ACT Research remains fuel agnostic, reporting and analyzing a variety of alternative power solutions. It is ACT’s contention that fleets know their specific operations better than anyone else and should use that information to make their own decision. Additionally, it is worth noting that, like any other alternative to traditional technologies, EVs are typically being compared to the known baseline of diesel powered internal combustion engines.
We started by contacting Greater Indiana Clean Cities for assistance in locating a fleet we could contact for an in-depth interview. GICC is a resource we have previously used. They connected us with Cummins Inc, who answered questions and invited us to visit their test track to drive electric vehicles.
The day of the visit was overcast, cold, and blustery, with rain threatening. Nevertheless, it was a great opportunity. What follows are our observations, conclusions, and answers to our questions. We have also included some analogies that we considered as we think about how the possible transition to electric commercial vehicles might actually take place.
OBSERVATIONS:
We talked with product and service engineers within the Cummins New Power business unit. These engineers were tasked with matching commercial electric vehicle performance with customer needs and wants. They have been working on the development of battery electric power systems. They were not working on cab design, suspensions, brakes, etc. Their concentration, again, was on the power system.
At the test track facility, the engineers could replicate many different situations that vehicles would encounter in real-world operations. Besides real-world testing at the track, Cummins can simulate practically any road in North America. Test track work is intended to confirm that the truck will perform as predicted in the dynamometer lab tests. As an example, electric truck performance on hills can be evaluated to determine how it compares to a gas- or diesel-powered counterpart.
Upon arrival at the track, we were escorted to an electric bus for a briefing. The bus heater was powered by the same batteries that power the vehicle. Novices to the EV world might perceive that you could not heat a school bus with battery power. That perception is wrong. The bus was warm to the point that one could remove a coat and feel comfortable. Additionally, the electric bus was quiet and did not vibrate or smell (emissions). And while these “missing” items were important to us, we can only imagine how critical it would be for a full-time driver of any commercial vehicle to do a day’s work and be able to return home with hearing, muscles, lungs, and clothing in pretty much the same condition as when they left the house to start their day.
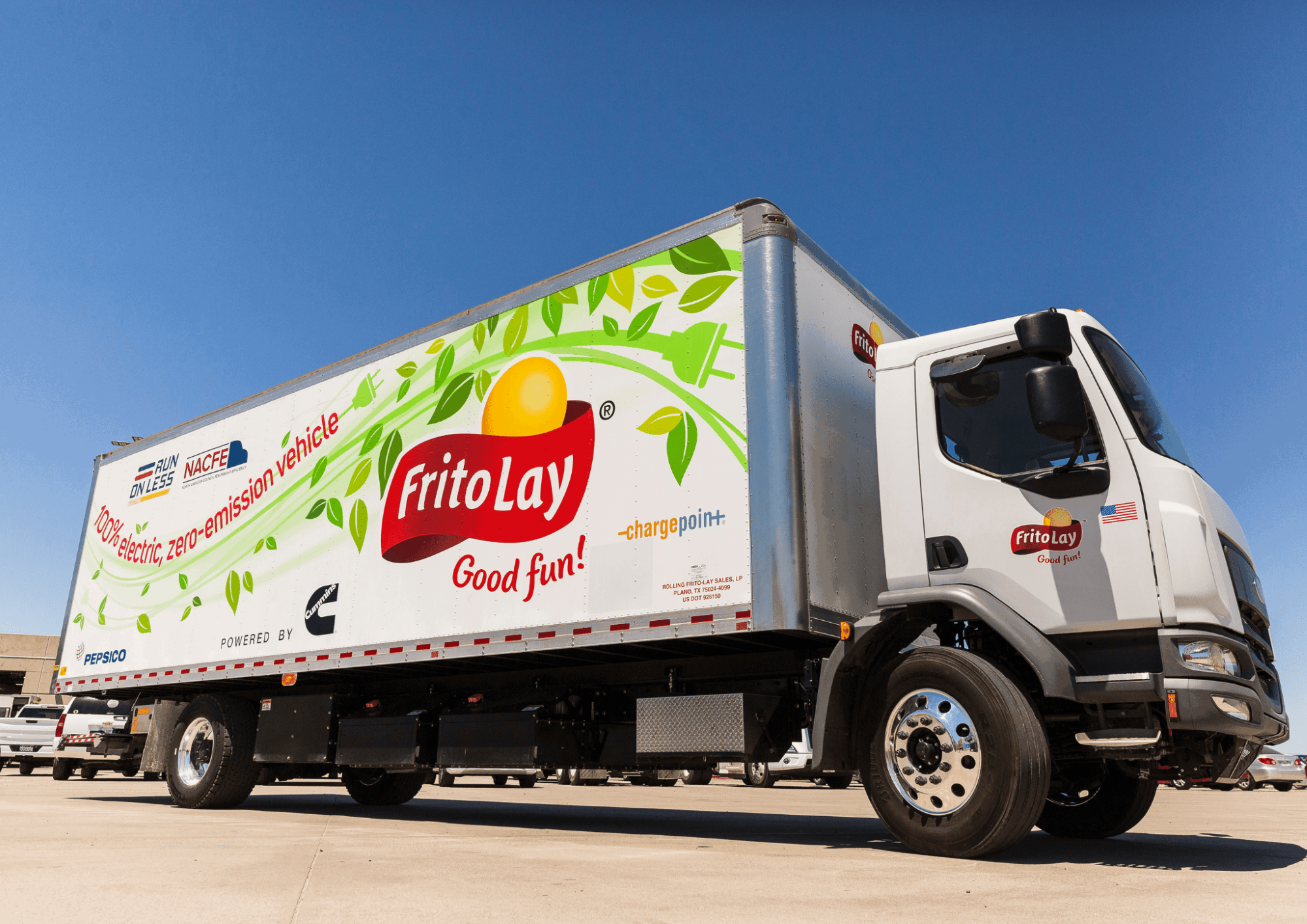
The next EV we encountered was a box truck. The only outward signs that the truck was electric were the decals and the battery packs on the bottom. Otherwise, it looked just like a diesel-powered truck. As an ACT associate slid into the driver’s seat and started the truck, those of us on the outside were surprised to hear a distinct “hum” coming from the vehicle. The sound we heard was the vehicle’s electric system. Electric motors run the air compressor for the vehicle’s air brakes, circulate fluids, and operate the cab air conditioning system and any other necessary functions that a truck would need.
The box truck was a production vehicle with a true EV dash, whose main feature was to tell the driver the state of the battery charge and remaining range. When evaluating a vehicle's mileage range, a number of factors must be considered, including the load, speed, degree of regeneration, topography, external temperature, and even the electrical accessory load. EV batteries undergo testing before use and have a +/- energy efficiency rating just like ICE units. Regardless, the driver gets plenty of indication of remaining battery energy/distance and when recharging is required. This is important for electric vehicles because the battery can be damaged by excessive discharge. According to engineers, the optimal charge level usually ranges from 20% to 80%. However, the truck manufacturer will determine exactly how the dash will indicate the remaining charge and miles to power exhaustion.
Starting the box truck was simple; turn a key on the steering column and a green light on the dash illuminated, signaling the truck was on. The acceleration of the box truck was very brisk, and the “hum” was not audible in the cab. A regular driver of this vehicle would most likely be completely satisfied by the performance. As with the yard spotter, cab heat in the box truck powertrain comes from the energy in the battery. The box truck also has a regeneration system, At first, the regenerative effect was foreign and took some getting used to. The feature would probably come in handy for delivery in congested big city traffic. Analogous to the use of an engine brake in a diesel truck, the regen feature is designed to optimize brake life and maximize battery charging. While electric drivetrains can be designed to produce instant torque, this is not necessarily the case for all electric vehicles. Rather, the amount of power (torque) that is applied by the electric motor at launch can be controlled. In fact, emulating gas or diesel engine torque can result in the driver’s perception that the new electric truck has exactly the same performance. As an added benefit of controlling the torque, excessive tire wear is eliminated. When asked about customers’ feedback on battery-powered truck demonstrations, the Cummins employees responded that reactions were overwhelmingly favorable.
For our next experience, we hopped aboard a yard spotter, a vehicle that moves trailers around a trucking terminal. Terminal tractors or yard spotters can be found in distribution centers and ports, as well. Few are ever licensed for use on the road, and they spend their days moving trailers around freight yards. For those not familiar with a terminal tractor, there is a big sliding door in the back of the cab where the operator can step out to hook up/disconnect air and electric connections of trailers being moved or spotted.
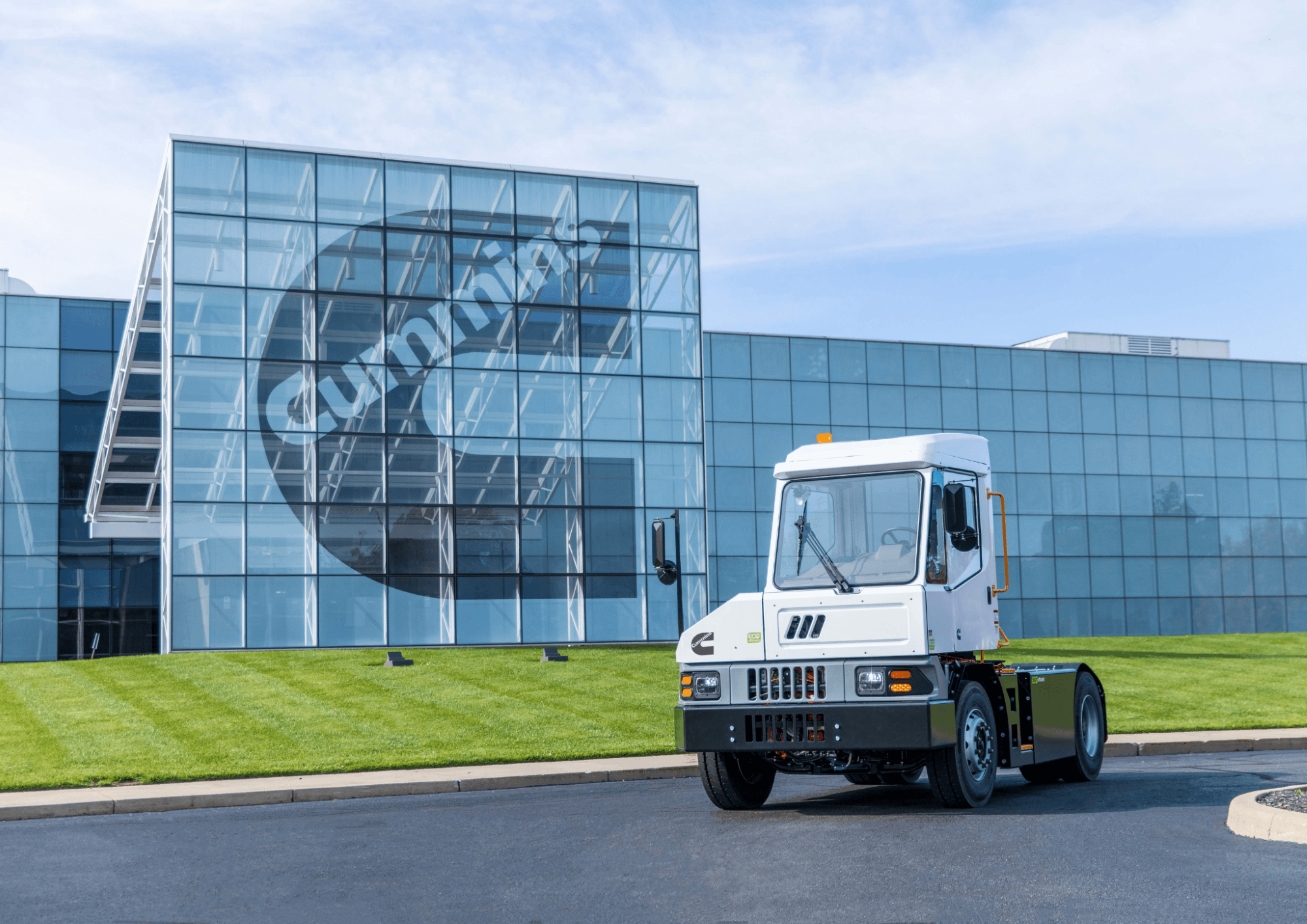
During this ride, we sat in the jump seat and questioned the Cummins engineer as he drove the vehicle. The dashboard contained the remnants of the diesel instrument panel, which the tech was using to make sure the air brakes had sufficient air pressure. Next to the old panel was a new electronic panel about the size of a large iPad. It displayed readings from the sensors on the battery and power systems. The engineer proudly explained that the warm and cozy cabin was heated solely from high voltage powered e-heaters and not the coolant system.
Contrary to what one might think, these electric trucks had a “cooling” or conditioning system. If one were to take a cursory glance with the trucks hood open, one could easily mistake a coolant reservoir container filled with antifreeze for a coolant recovery bottle on a traditional gas or diesel powered truck. The coolant reservoir bottle is part of an overall system to maintain a desired temperature for the battery and related hardware. If a driver needs heat in the cab, the power source is energy in the battery itself, and not from any cooling system. Remember the “hum” mentioned when standing next to an electric truck that is in operation? The hum is from the pumps circulating coolant around/through the battery and related hardware, as well as for the air compressor to maintain air pressure for the truck air brakes. The key point is that electric trucks have a cooling system to maintain the battery and related components at a near- optimum temperature. Cab heat, if used, does not come from the cooling fluid, so as not to have the battery temperature maintain system run at too low a temperature. Battery electric vehicles can operate at the same environmental ambient temperatures as today’s diesel engine products. Even though it was a winter day, the battery has a thermal management system that keeps operation at its best efficiency and effectiveness. Without the thermal management system, the battery would experience reduced performance and a shortened useful life.
During the short ride on the test track, we noted acceleration was brisk and cab noise essentially non-existent. There was no sense of excessive speed. When the engineer demonstrated the regeneration feature, it was obvious that it engaged. The sensation was as if the vehicle brakes were partially applied. At first, this seemed like a drawback to the system, but after the engineer explained a few things, it all made sense. The vehicle was designed this way to emulate the duty cycle of a yard spotter, which includes quick movement of a trailer from one spot to another ---- accelerate, brake, and back into another spot and/or leave the trailer in another location.
Driver pre-trip inspections are critical to the safe operation of the commercial vehicle, regardless of their power source. Clearly, the specific items to be checked will differ for EVs, but are no more onerous. Fleets will need to ensure that the power system is operating within the specified tolerance range and has sufficient fluid with no leaks before it departs. Similarly, as with an ICE, the driver needs to be observant of warning signals and take appropriate action.
A final comment about N/V/H (engineering abbreviations for Noise, Vibration, and Harshness), things that a driver can hear, feel, and sense. In some ICE trucks, the driver or perhaps the maintenance department can set a diesel engine’s idle speed within limits. This adjustment is a way to stop the mirrors from shaking at idle. No such adjustment feature is required on the battery-powered trucks we drove. The mirrors were rock solid and the noise in the cab was nonexistent. When given a choice of ICE or EV in actual-use tests, drivers would take the electric vehicle, citing their quiet, smooth, and vibrationless operation.
CONCLUSIONS:
What did we learn and what conclusions did we draw during our short time at the test track? First, while the industry doesn’t have the nearly 90 years’ experience running battery powered trucks as it does with diesels, the first box trucks were battery powered and replaced the horse and wagon. That said, the industry can probably learn something new every day as electric trucks go into service. Second, everyone has an opinion, and sometimes the “facts” to support those opinions can get a little distorted. We were after the “facts” from the people who should know. We’re comfortable that ACT got the facts from unbiased professionals. Cummins has become a supplier of both traditional and nontraditional power sources, including diesel, gasoline, natural gas, propane, and hydrogen. Again, we attempted to provide some observations and answers to questions. So, here are some basic conclusions:
- Lithium EV batteries must be maintained/operated within a certain temperature range to maximize their use. There is a “sweet spot” for battery usage. Find it and use it.
- From instrumentation to performance, design, and application, engineers are doing their utmost to make the transition from ICE equipped trucks to battery-powered trucks as seamless as possible for drivers and maintenance personnel. Once Cummins’ engineers get the powertrain basics correct, those who design chassis, as well as those in production, can build on the solid foundation. This work is being done holistically, with input from and consideration of those on the front-lines, including drivers and maintenance technicians, as well as others along the freight industry and supply chain.
- Since 2027 diesel engine emissions standards are still being formed - the result, the cost of compliance is still a wild card. As a result, cost comparisons between ICE and battery powered electric trucks are a bit of a moving target. What is clear is that time and experience will fill in the blanks, and a lower TCO will increase the likelihood of EV adoption.
- There are no emission meters in electric trucks. An operator has no idea how much reduction in emissions there is from operating an electric truck versus an ICE-powered truck. We’ll leave all those measurements and well-to-wheel comparisons to the scientists. From a driver’s perspective, the electric vehicle can get the job done, just as ICE-equipped trucks do.
ANALOGIES:
Again, we all are entitled to our own opinions as to whether electric trucks will come to fruition in large numbers and be cost-effective or not. But as one forms his or her opinion, stated below are some thoughts about timing.
- History tells us that early perceptions of cell phones were mostly negative. They were big and bulky, cell towers were few and far between, calls got dropped, phones were very expensive and the charge and battery life left a lot to be desired. Today, smart phones are simply indispensable.
- When was the last time you bought film for your camera? You remember that expensive camera you bought, the one with the optional telephoto and wide-angle lenses? Ever shown a picture of a family outing on your phone to a friend or send it to them via the internet, or are you still waiting for your prints to be developed and printed?
- Why do most people drive cars with automatic transmissions? In the 1950s, people believed: they cost a lot more, engines need more horsepower for the automatic to equal a manual, they use more fuel than a manual, they cost more to overhaul, the vehicle will weigh significantly more, etc., etc., etc. Nowadays, drivers who know how to drive a vehicle with a manual transmission are as rare.
- A similar phenomenon took place in the commercial vehicle industry. Automatic (or automated manual) transmissions were OK for refuse trucks, but no red-blooded Class 7 or 8 truck driver was going to drive any automatic transmission-equipped truck. Arguments against automatics were pretty much the same for cars, though the stakes were arguably higher: they weighed more, cost more, were not as fuel-efficient, needed more frequent overhauls, had lower resale value and just weren’t very macho. So how did the automated mechanical transmission sneak in? Thanks to the real facts, today, automated mechanical transmissions are found in somewhere around 90% of new tractors.
- Finally, it took more than 40 years from the introduction of the diesel-powered truck (1931) until it had more than 50% share of the new heavy-duty truck market (the 1960s). Won’t it take that long for the conversion to electric trucks to take place? The fact that there was no interstate highway system to take advantage of the weight hauling ability of the new diesel, few diesel fueling stations, few compatible driveline options, few repair facilities and the fact that they cost more than gas really had no bearing on the time for transition. How long it will take electric to displace ICE as the majority CV power source is up for debate, but the fact that the clock is ticking is indisputable.
Change takes time. But what seems to be changing is the time it takes for change to occur. From the examples above, we might conclude that the time to change in today’s environment is compressed. We can all do a TCO (Total Cost of Ownership) analysis to get a number when we think about change, but when you possibly add in environmental, regulatory and political considerations, the end result might not be what you first expected. Perhaps we really are “charging” into tomorrow.
REFERENCES:
In preparation for this article, ACT spent some time reviewing material available on the internet, as it pertains to electrically powered trucks and buses. They proved quite interesting in helping us prepare our questions to discuss with battery powered development engineers. You may want to review them for additional information.
Cummins Inc.
Run on Less: https://www.youtube.com/watch?v=3o_6ikBP_fc Trusted because it is tested: https://www.youtube.com/watch?v=oCdBUqHWkV0 Preventech:
https://www.youtube.com/watch?v=5z1HgoPaZlM&list= PLLrQbKwPujUsMd7_KchNvAGvEkiProQwl&index=12
Introducing Powerdrive:
https://www.youtube.com/watch?v=tA0V1xGjD- 4&list=PLLrQbKwPujUsMd7_KchNvAGvEkiProQwl&ind ex=2
Purolator:
https://www.youtube.com/watch?v=zvLN5b28jgk&list=P LLrQbKwPujUsMd7_KchNvAGvEkiProQwl&index=3
Worksite:
youtube.com/watch?v=uY9hVl_69BU&list=PLLrQbKwP ujUsMd7_KchNvAGvEkiProQwl&index=9
School bus:
https://www.youtube.com/watch?v=TDiEKr_PWNo&list= PLQfwssCUSc6kmOtutXPMx6LmS-ba53Ry-&index=9
Greater Indiana Clean Cities:
https://greaterindiana.com/ information@greaterindiana.com
Advantages of H2 ICE we took away from our conversation with Cummins Inc. engineers
- Reduce the amount of harmful pollutants as byproducts of combustion
- Fuel tanks are the same and carry the same part number as the H2 tanks used for H2 FCEVs
- Air intake systems will be the same as for diesel and NG-fueled units
- Will use DEF and SCR for NOx controls
- The solution will not use a three-way catalyst for NOx control
- Extended maintenance intervals beyond where the industry is today with NG engines and current diesels
- Not in competition for rare metals
In part 1 of this series, ACT provided in-depth observations on battery-powered cargo trucks and yard tractors. The goal of the series is and was to provide first-hand observations based upon discussions with engineers and ride alongs with prototypes to answer reader questions. What are these vehicles really like to operate? How might they fit into your operations?
Part 2 concentrates on what hydrogen-fueled (H2) internal combustion engine (ICE) alternatives have to offer. What can one expect and what are the unknowns? To prepare, we spent time with several Cummins development engineers who shared with us the technical aspects of an H2-fueled ICE, but, moreover, where they see it being applied in the future.
There are all sorts of fuels in use today—diesel, natural gas (NG), gasoline, and propane to name but a few. Why would one consider H2 as a fuel for an ICE? There are no carbon molecules in H2. Consider the alternatives: they all contain varying amounts of carbon and in the combustion process of an ICE, the carbon gets released or combined with other elements. So, if we use zero carbon H2 as a fuel, we are home free, right? We don’t have to worry about any pollution whatsoever. Wrong! Anytime you burn a fuel in an ICE you are mixing that fuel with air that contains a host of other elements. The result of that process, the burning of fuel in the combustion chamber, results in nitrogen oxides and a host of emissions, including water. There is no free lunch here. But, if you start with the cleanest fuel you can find and can largely control the timing and temperature of combustion, you have the opportunity to reduce the amount of harmful pollutants as byproducts of combustion. Thus, H2 as a fuel has a real advantage.
Cummins engineers are starting with the 15-liter diesel engine as the base for the development of a 15-liter H2-fueled, heavy-duty (HD) truck engine, as there is no need to reinvent the wheel—just adapt the base diesel engine for an alternative fuel. The base engine is of a proven design, diesel with NG engines or H2 ICE can be produced on the same engine assembly line with no production constraints, and it greatly simplifies the engine installation for the truck manufacturers. With minor variations, the same 15-liter engine “platform” fits into existing truck models. Targets would be for 500 horsepower with 1,850 lb.ft. of torque. The 15-liter diesel engine serves as the base, while a unique design cylinder head utilizing direct injection of H2 is a distinctive part of the design. The difference for truck manufacturers is the mounting of the “fuel” tanks. OEMs already have experience with mounting NG tanks, and those for H2 are very similar. In the end, costs are ultimately controlled for the truck manufacturers and customer.
Consider the impact of the new, impending diesel emission legislation on the traditional diesel engine and OEM installations. If an NG-fueled truck has a 2,000-pound weight exemption under the existing law compared with a diesel, an H2-fueled, ICE-powered truck will need a 2,500-pound weight exemption to account for the incremental weight of the H2 fuel tanks. The H2 fuel tanks are very similar to NG tanks, but the tank assembly weighs 500 pounds more than an NG fuel tank assembly because of the increased wall thickness of the H2 tanks. CNG tanks operate a maximum of 3,600 pounds per square inch (PSI). H2 tanks will operate at a maximum pressure in the neighborhood of 10,000 PSI. The same safety precautions, or very similar ones, will apply to service shop bays and using H2-fueled vehicles in tunnels, warehouses, and manufacturing facilities. As a side note, the H2 ICE fuel tanks are the same and carry the same part number as the H2 tanks used for H2 fuel-cell electric vehicles (FCEVs). Again, this simplifies things for the truck manufacturers. Regardless of the increased weight of the tanks, approximately 70% of all trucks on the road cube out (the trailer doors are closed when the trailer is full) and the vehicle doesn’t approach 80,000 pounds, while approximately 30% of the trucks on the road gross out (the trailer is filled with product until the combined tractor/trailer weight is 80,000 pounds).
H2 ICE requires no special air intake system compared with an H2-fueled FCEV system. The FCEV requires a sophisticated air intake system to keep air contaminates from going into the membrane. Thus, the air intake systems for H2 ICE trucks will be the same as for diesel and NG-fueled units, another plus for H2 ICE vehicles from the truck OEM ease-of-installation point of view.
The H2 ICE utilizes a spark ignition system very similar to that on an NG-fueled engine, which mixes the fuel and air outside the combustion chamber. The H2 ICE uses direct injection of the H2 into the combustion chamber with a spark plug ignition system. This approach gives the H2 ICE a performance advantage over an NG system. If we were to read the performance specifications of an NG, H2 ICE, or diesel engine we could “spec” all three with the same horsepower and torque. How they perform will be different. We could have a theoretical discussion about it, but suffice to say a driver measures “performance” by the seat of their pants. How quickly does the engine respond? What drivers will find, if we use the current diesel of a given horsepower as a base, is that an equivalent horsepower H2 ICE will deliver the same power and torque performance. Although the H2 ICE is spark ignited, it does have direct fuel injection into the combustion chamber, which gives it an advantage over NG. Further, the H2 ICE is more like a diesel with its lean burn design. An NG engine is more stoichiometric, meaning the fuel/air ratio is fixed. The H2 ICE will be a lean burn design just like a current diesel, allowing for reduced emissions. Regardless of the perceived “performance” of the three engines under consideration, they are all adequate for today’s drivers.
The Cummins H2 ICE solution will use DEF and SCR for NOx controls. It will not use a three-way catalyst for NOx control. With an H2 ICE’s spark ignition and direct injection, cold weather starts will be better than with diesel. Based on the lean burn design and the fact that direct injection will be used, engineers hope they will be able to extend maintenance intervals beyond where the industry is today with NG engines and current diesels. We don’t yet know what will be required with the new emission diesels.
Although the current perception may be that battery-powered trucks will dominate and that H2 ICE-powered trucks will be in the minority, engineers we spoke with might not share that view. Their perception is the current electrical grid in the US is not sufficient to support a major shift to automobile EVs, nor medium-duty (MD) or HD trucks. Major upgrades in the electrical grid will be needed. H2 ICE may be the dominant solution to reducing emissions, explaining why Cummins is developing its 6.7-liter H2 ICE.
Regarding the North American (NA) market, Cummins engineers believed that hydrogen-fueled truck usage would first occur along the Canadian border. Shortly after our last roundtable discussion, Cummins announced they would supply a 35-megawatt (MW) electrolyzer system to Linde for the production of green hydrogen at Niagara Falls, New York. The electrolyzer system splits water into oxygen and hydrogen. The end product of hydrogen can be stored as a compressed gas or liquid. Outside of NA, the H2 ICE has found a greater degree of acceptance. Production of the H2 ICE is targeted for the NA market in 2027, with demo units available in 2024. Engineers believe H2 ICE will complement the NG engine in the market because of the extensive NG support network in place. H2 ICE will start slow because of a higher purchase price and less dense fueling network, but the market will grow over time with the anticipated support for hydrogen fuel.
Will current diesel fuel suppliers begin distribution of hydrogen fuel in the months ahead? Cummins’ engineers believe they will, as “fuel suppliers sell molecules and not a specific fuel.” Fuel suppliers will make the conversion to selling hydrogen fuel as the purchase of diesel fuel is reduced. Remember, hydrogen fuel will be used in both H2 ICEs and FCEVs, particularly as it is believed the first adopters of H2 ICE trucks will use public fueling stations before they transition to behind-the-fence dedicated fueling stations for their fleets. H2 ICE trucks can be fueled at the H2 rate of 2.5 kilograms per minute. This implies it would take 32 minutes to fuel an HD truck from empty. Hydrogen fuel will probably be in a compressed state, similar to the favored approach with today’s NG-fueled trucks. Liquid H2 fuel would encounter the same cost penalty as liquid natural gas (LNG) and, thus, would not be favored.
Another advantage of the H2 ICE is that it is not in competition for rare metals currently required for battery-powered vehicles. Further, the H2 ICE doesn’t get politically involved with who controls the vast majority of rare metals and whether they are friend or foe.
Replacing diesel truck engines won’t occur overnight. There are many viable alternatives, and on the road to lower emissions, each technology has its strengths and weaknesses. There is no one magic answer, and Cummins is preparing a number of viable alternatives for its customers.
How does ACT view the future of powertrain alternatives?
While ACT remains fuel agnostic, and believes fleets know their operations better than anyone else, we also recognize ICE costs will rise as increased emissions regulations are globally adopted, and tougher regulatory standards for ICE will lead to a more favorable TCO for CEV. Most CVs are working in competitive situations, so questions on operating costs are fundamental. Will each powertrain alternative—EV, FCEV, H2 ICE, etc.—offer varying degrees of ROI? Yes. And, of course, this depends on each application's unique duty cycle. ACT Research uses a bottom-up approach, analyzing component costs, operational costs based on duty cycles, fuel costs, maintenance costs, taxes, infrastructure, and more.
FCEV Links:
Want to read more about Accelera’s FCEV efforts?
Destination Zero: Introducing Destination Zero - YouTube
Hydrogen Fuel Cells and Cummins: https://youtu.be/0miaOAfrS5Y
Accelera: https://www.youtube.com/watch?v=T5z8GfNenok&pp=ygUSRnVlbCBDZWxsIEFjY2VsZXJh
Passenger rail: https://www.youtube.com/watch?v=ADhCSQuvKNg&pp=ygURY3VtbWlucyBmdWVsIGNlbGw%3D
Accelera Landing Page: https://www.accelerazero.com/fuel-cells/pem
Make a splash with H2 tech: https://www.youtube.com/watch?v=DSnXcwuwOJU&pp=ygUYY3VtbWlucyBmdWVsIGNlbGwgZW5naW5l
The Future of clean power: The Future of Clean Power with Cummins - YouTube
Top Electric (not Cummins, but pretty good):This Hydrogen Truck Will DESTROY All Current Trucks! - YouTube
H2 Rescue: https://www.youtube.com/watch?v=_QemCBiEipk
H2 Rescue-Flyer (accelerazero.com)
H2Rescue | Fuel Cell Emergency Relief Vehicle Demo | Accelera (accelerazero.com)
The Cutting-Edge Potential of Hydrogen Fuel Cell Emergency Vehicles - YouTube
H2 the Rescue | How a Hydrogen-Powered Rescue Truck Helps First Responders - YouTube
H2 ICE Links:
Want to read more about Cummins’ H2 ICE efforts?
https://cdllife.com/2022/werner-to-buy-500-cummins-hydrogen-engines/
https://www.truckinginfo.com/10170361/cummins-debuts-15l-hydrogen-engine
https://www.ttnews.com/articles/hydrogen-likely-be-next-fuel-trucking
https://www.fleetequipmentmag.com/cummins-hydrogen-combustion-engine/
https://finance.yahoo.com/news/cummins-demonstrate-hydrogens-potential-reduce-152011738.html
https://www.motorbiscuit.com/cummins-moving-away-diesel-engine-lineup/
https://www.freightwaves.com/news/cummins-adding-hydrogen-electrolyzer-manufacturing-in-us
BEV Links:
In preparation for this article, ACT spent some time reviewing material available on the internet, as it pertains to electrically powered trucks and buses. They proved quite interesting in helping us prepare our questions to discuss with battery powered development engineers. You may want to review them for additional information.
Cummins Inc.
Run on Less: https://www.youtube.com/watch?v=3o_6ikBP_fc Trusted because it is tested: https://www.youtube.com/watch?v=oCdBUqHWkV0 Preventech:
https://www.youtube.com/watch?v=5z1HgoPaZlM&list= PLLrQbKwPujUsMd7_KchNvAGvEkiProQwl&index=12
Introducing Powerdrive:
https://www.youtube.com/watch?v=tA0V1xGjD- 4&list=PLLrQbKwPujUsMd7_KchNvAGvEkiProQwl&ind ex=2
Purolator:
https://www.youtube.com/watch?v=zvLN5b28jgk&list=P LLrQbKwPujUsMd7_KchNvAGvEkiProQwl&index=3
Worksite:
youtube.com/watch?v=uY9hVl_69BU&list=PLLrQbKwP ujUsMd7_KchNvAGvEkiProQwl&index=9
School bus:
https://www.youtube.com/watch?v=TDiEKr_PWNo&list= PLQfwssCUSc6kmOtutXPMx6LmS-ba53Ry-&index=9
Greater Indiana Clean Cities:
https://greaterindiana.com/ information@greaterindiana.com